決意を新たに地球規模の課題に取り組む
豪雨による洪水や熱波に起因する山火事など、地球温暖化による自然災害が世界各地で多発し、社会・経済に甚大な影響を与えています。多くの国がCO2削減目標を引き上げ、国境炭素税の導入など厳しい規制に乗り出し、日本は「2050年カーボンニュートラル」を宣言しました。企業にとっても対岸の火事ではなく、カーメーカーは製品のライフサイクル全体で多くのCO2を排出していることから、BEVやFCEVなどゼロエミッション車へのシフトを急速に進めています。サプライヤーに対しても連携要請は強く、CO2削減量が発注条件となる厳しい現実がすぐそこまで来ています。
当社は、1993年に初の環境活動5カ年計画「第1次環境取組みプラン」で本格的に環境活動を開始。2016年2月には、6つの高い目標からなる「TG2050環境チャレンジ」を公表し、その一つとして「脱炭素社会」を明確に打ち出しました。これを契機に、非生産時の電源オフ徹底や省エネ設備への切替、エネルギーロスの低減といった日常的な改善を工場全体で推進する「TG-ESCO」活動のほか、廃棄物や水使用量の低減、再生可能エネルギー(以下、再エネ)の導入などに、各部署が積極的に取り組んでいます。カーボンニュートラルの実現に向けては、CO2を排出しない材料開発やモノづくりの仕組みを大きく変える革新的な技術開発などをいくつも組み合わせていく必要があります。これらを並行して進めていくために、他企業との協力など様々な手段を取り入れスピード感を持って取り組みを進めていきたいと思います。
ゴム・樹脂の高分子技術を有する専門メーカーである当社は、カーボンニュートラルの実現に向け、業界およびグループをリードする決意で取り組んでいきます。
■環境活動の考え方
■TG2050環境チャレンジ
Targets 50&50
当社は2021年4月の「ESG説明会」で2050年のカーボンニュートラルを改めて宣言し、経営の重要課題と位置付けました。そして、2030年までの中間目標としてCO2排出量を50%削減(2013年度比)し、再エネ導入率を50%に引き上げる「Targets 50&50」を発表しました。この目標は、カーボンニュートラル実現のためのマイルストーンとして必達すべきものであり、仕入先を含め豊田合成グループが一丸となって活動を推進しています。
ゴム・樹脂が循環する仕組みづくり
製品のライフサイクル
2050年のカーボンニュートラル実現は、モノづくりの上流となる材料・部品の調達、そして使用後の廃棄段階まで踏み込み、製品のライフサイクル全体でCO2排出量の削減を可能にする革新的な内容をいくつも組み合わせなければなりません。
ゴム・樹脂の専門メーカーとして
当社はゴム・樹脂を専門とする高分子メーカーとして、技術力やノウハウをもって、自動車の軽量化や環境問題の解決に貢献してきました。これからはカーボンニュートラルという地球規模の課題において、ゴム・樹脂製品のライフサイクル全体で脱炭素を実現するという社会的な役目も担っていきたいと考えています。例えば、CO2排出量の少ない自然由来プラスチックの活用など、プラスチック業界とも連携しながら、ゴム・樹脂が循環する仕組みづくりに挑戦していきます。また、これまでは安くて品質の良い製品をお客さまにお届けすることが付加価値につながりましたが、これからは製品ごとのライフサイクル全体におけるCO2排出量の低減によっても製品価値の向上を図っていきます。
こうした環境への取り組みと、会社の持続的成長を両立させるため、CASE、MaaS(Mobility as a Service)への対応を含め、BEV・FCEVに向けた製品開発も加速していきます。当社には、社外取締役をはじめ環境を専門とする有識者も多く、総力を結集してスピード感と実効性を重視しながら取り組んでいく考えです。
全社横断のプロジェクトで活動を推進していく
体制の強化
2021年6月に「カーボンニュートラル・環境推進部」を開設し、推進体制の強化を図っています。活動の要となる「環境委員会」は、2019年に海外統括会社社長を含めた「グローバル環境委員会」へ、2021年には「カーボンニュートラル・環境委員会」へと領域を拡大し、開発設計から生産まで全社横断のプロジェクトとして、一気通貫で取り組む体制を整えました。さらに持続可能な活動を推進していくために、環境意識の高い企業風土や人づくりにも力を注ぎます。
「環境のTG」へ
当社の理念である「限りない創造 社会への奉仕」は、カーボンニュートラルの取り組みを根底で支えるものです。これからはゴム・樹脂分野でCO2削減をリードする「環境のTG」として、持続可能な社会に貢献できる企業を目指していきます。
■カーボンニュートラルに向けた中長期シナリオ
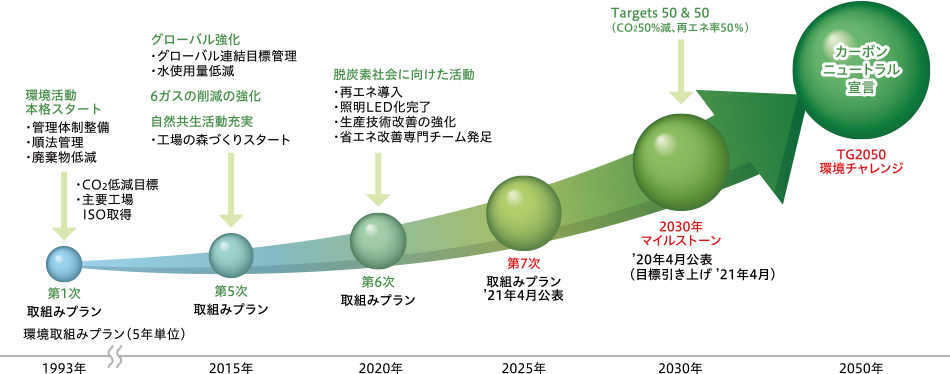
2050 カーボンニュートラルのロードマップ
活動領域を拡大
2020年度の当社のサプライチェーン全体の温室効果ガス排出量は155.3万t-CO2です。そのうち、当社の事業活動による直接的な温室効果ガス排出量(Scope1)が9.9万t-CO2、購入電力の使用といった間接的な排出量(Scope2)が36.7万t-CO2、原材料の調達・通勤や出張・製品の使用や廃棄といったScope1・2以外の排出量(Scope3)が108.7万t-CO2です。
当社は、自社の生産に伴うCO2排出(Scope1・Scope2)をゼロにする活動として、約5年前に4つの柱を打ち出し、早い段階での目標達成を目指してきました。現在は、LCA全体でカーボンニュートラルを実現するため、サプライチェーン排出量の約7割を占める生産前や生産後(Scope3)まで範囲を広げ、様々な活動を強化・拡大しながらCO2排出削減に全力を注いでいます。
ゼロを目指す、4つの柱
柱Ⅰ 日常改善
工場での地道な省エネ活動に加えてカーボンニュートラル・環境推進部と工場のメンバーが一体となってエネルギーロスを現地現物で調査し、改善方法の検討から対策まで行います。例えば、蒸気のロスを減らす熱回収ヒートポンプの導入、圧縮エアーの圧力損失の削減などが挙げられます。
柱Ⅱ 生産技術革新
CO2を極力排出しない工程を徹底的に追求しながら、省エネ工程設計や省エネ工法開発など、モノづくり現場の革新による高付加価値工場を目指します。また、IoTやAIを活用したトラブルの未然防止、廃材の再利用などの技術革新も進めています。
柱Ⅲ ユーティリティー設備更新
生産工程に使われる動力源「ユーティリティー設備」について、老朽化した設備は生産支障リスクを抱え効率面でも劣るため、計画的に更新しています。また、蒸気エネルギーの動力源を重油からLNGに置き換えるなど、低CO2設備への更新も計画的に行っています。
柱Ⅳ 再エネの導入
2007年度から太陽光発電設備の導入を開始しました。2019年度からは、新工場の太陽光発電設備の設置を標準化するなど、再エネを積極的に導入しています。
■カーボンニュートラル実現に向けた計画
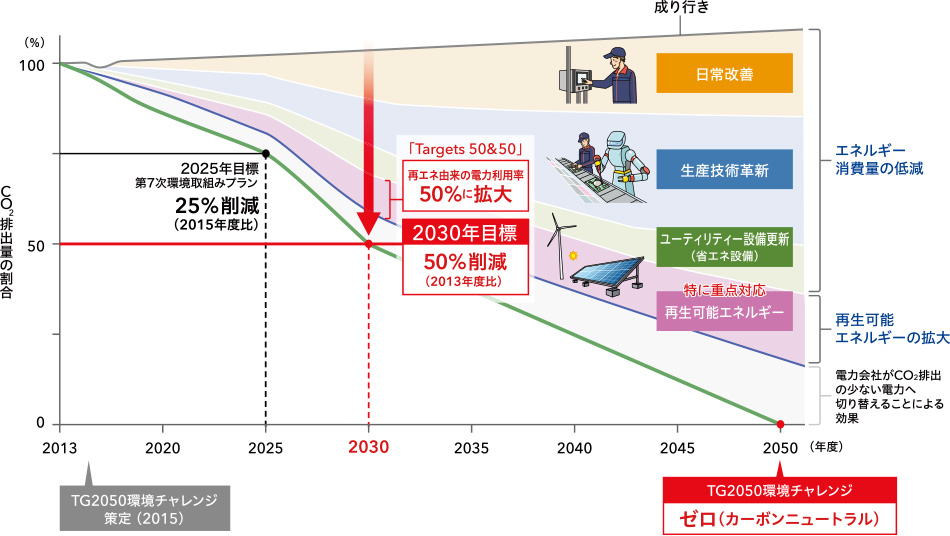
技術力を結集した製品開発でCO2排出量ゼロに貢献
これまでは安くて品質の良い製品をお客様にお届けすることが付加価値につながりましたが、これからは循環型社会に貢献できる製品開発が重要となります。ゴム・樹脂の高分子メーカーである当社は、モノづくりにおける原材料・購入部品の段階から廃棄に至るまで、製品のライフサイクル全体において、材料開発、軽量化、プロセス革新、100%リサイクルなど、様々な技術力を結集してCO2排出量ゼロを目指します。
CO2削減への挑戦
【材料】原油由来から自然由来へ
軽くて加工しやすいプラスチックは、自動車の軽量化に大きく貢献する反面、自然環境下では分解されにくく廃棄時に燃やすとCO2を排出するといった課題も抱えています。プラスチックに「持続可能性」という新しい付加価値をもたらすため、非石油の新資源として、バイオマスプラスチックや生分解性プラスチックなど環境負荷の低いプラスチック開発に積極的に取り組みます。
【コア技術】セルロースナノファイバー
木材から繊維を取り出してナノ化する自然由来セルロースナノファイバー(CNF)は、鋼鉄の1/5の軽さと、5倍以上の強度を両立する「低比重・高剛性」が特徴です。軽量化によるCO2排出削減効果があり、また、自然由来のため生育時にCO2を吸収しており、廃棄時に燃焼してもトータルとしてCO2が増えることはありません。当社では自動車部品の適用を目指し、セルロースナノファイバーとプラスチックの複合材料の開発を進めています。
【設計】易解体
廃車になった自動車は鉄、ガラス、樹脂など原料に戻すことで再利用されますが、1台あたり約140kgの部材が再利用できずに廃棄されています。理由の1つに、部材を解体できないことが挙げられます。そこで当社では、モノづくりの上流である設計段階から、パーツの固定方法を見直したり、解体し易い構造を採り入れたりして、廃棄物低減やリサイクル向上に取り組んでいます。
【工程】表面処理の革新
意匠性や外観品質を高める表面処理技術の塗装・めっき工程は、エネルギー消費によって多くのCO2が発生します。そこで、フィルムの活用や、めっきレスで外観品質の優れた樹脂材料への変更など、表面処理プロセスの革新を目指します。
【工程】ゴム加工革新
一般的にゴムの加硫工程では、多くの蒸気や熱を加える必要がありますが、その際にエネルギーのロスが生まれていることに着目し、脱蒸気加硫、常圧低温加硫、二次加硫レスといった革新的な工程づくりに挑戦しています。
■自社だけの活動(Scope1・2)だけでなく、製品ライフサイクル全体に範囲を拡大
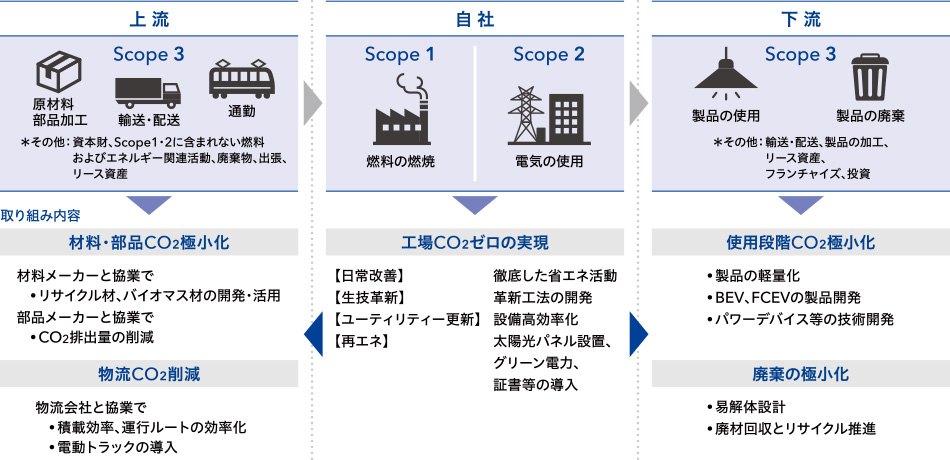
カーボンニュートラルに向けた具体的な取り組み
製品開発の取り組み
樹脂製品
環境負荷低減と収益確保を両立する製品開発を推進しています。例えば、かつて金属製が主流だったフューエルフィラーパイプを樹脂製に材料置換することで50%の軽量化を実現しました。現在は、海外拠点に樹脂フューエルフィラーパイプの生産工程をグローバル展開しながら、環境負荷低減に貢献しています。今後も、燃料系部品で長年培ったノウハウを活かし、BEV・FCEV向けの技術開発や製品開発を推進するほか、当社の得意分野であるLEDを適用した車載製品を通じて自動車の省電力化にも貢献していきます。
■環境負荷低減と収益確保を両立する製品開発を推進
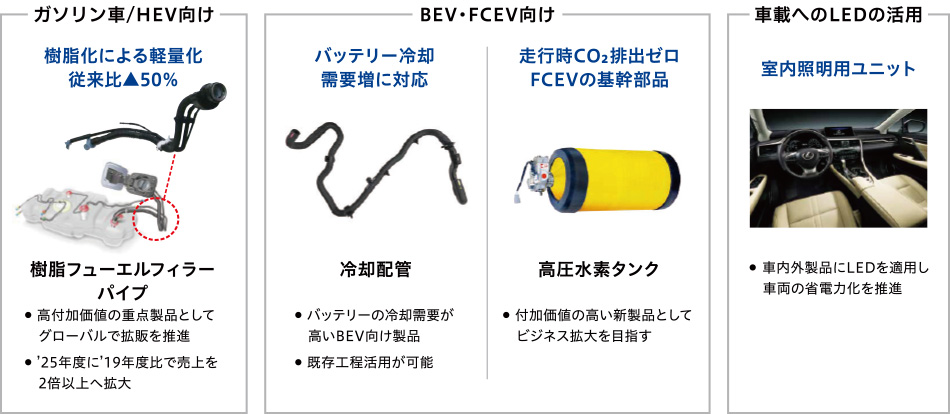
ゴム製品
長らく加硫ゴムの再生は難しいとされていましたが、当社はウェザストリップ製品の工程で排出された廃棄物をなくすことを目的に、加硫ゴムを再生する脱硫再生技術を約25年前に実用化。現在は再生ゴムのさらなる品質向上や、リサイクル率の向上を目指しています。脱硫再生技術のポイントは、脱硫工程内で適切なエネルギーを与え、ゴム分子の架橋点を選択的に切断することです。当社では2軸スクリューを構成するピースの最適形状や組み合わせによって、温度・圧縮力・せん断力をコントロールできるよう工夫しています。
2021年、森町工場では脱硫再生(リサイクル)工程の専用棟を設けることで、廃棄物(オープニングトリム)の4割以上が削減可能になりました。さらに、疲労軽減マットなどのリユース・リサイクル製品を開発し、ゴムの廃材や端材の活用を推進することで廃棄物の極小化を進め、ゴム分野におけるCO2排出量を着実に削減しています。
■脱硫再生の技術でゴムのリサイクルを実現
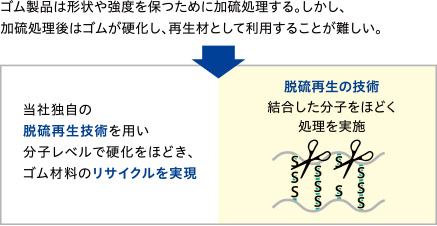
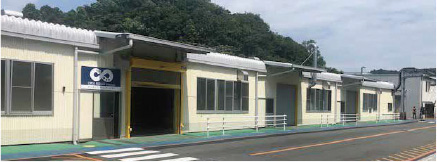
工場CO2ゼロに向けた取り組み
塗装工程のコンパクト化
外観品質が厳しく問われる塗装工程は環境管理が非常に重要で、塗装ブース内を常に一定の温度・湿度に保たなければなりません。そのため、塗装工程の消費エネルギーの40%を空調機器が占めていました。
そこで、加工前の素材を塗装ロボットに運搬する方法を「スライダー式」から、省スペースで運搬できる「ターン式+チルト機構」に変更することで塗装ブース体積のコンパクト化に成功、従来の半分以下に下げることができました。これによって空調機器の消費エネルギーが大幅に減少し、CO2排出量を約3割削減することができました。さらに、ロボット姿勢の簡素化によって塗装の歩留まりもアップするなど、品質のさらなる向上にもつながりました。今後は、コンパクトな塗装ブースを標準機としてグローバル展開していきます。
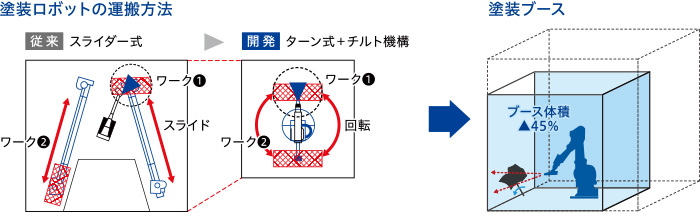
加硫シミュレーション技術の確立
ゴムの押出工程では、新しい工程を立ち上げる際、加硫させるときの時間や温度を変更しながら何度も試験・分析を行っていました。そこで工程や材料のデータを基に、事前に加硫のシミュレーションができる技術を確立。これによりトライ回数を大幅に減らすことに成功し、工程を立ち上げるまでに必要なエネルギーを削減することができました。
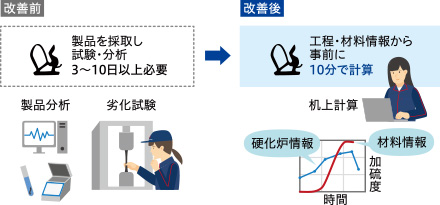
再エネの導入
2007年、従業員寮に太陽光発電を導入したのを皮切りに、グループ拠点に太陽光発電設備を設置してきました。2017年からは、環境委員会で導入計画と投資計画を立てるなど主導的な役割を担っています。2019年には新工場への太陽光発電設備の設置を標準化し、海外拠点も含めてグローバルに水平展開しています。また、いなべ工場では風力発電機も設置し、再エネの導入によって年間800tのCO2排出削減を見込んでいます。
■いなべ工場
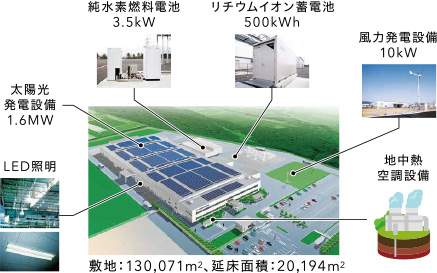
■豊田合成記念体育館エントリオ
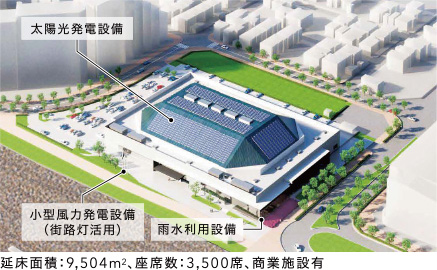