現在、世界では毎年約135万人もの方が交通事故で亡くなっています。交通死亡事故は、欧米や日本などでは減少しているものの、新興国など交通量の増大に対し、エアバッグをはじめとした安全装備の普及が追いついていない地域では増加傾向にあるためです。豊田合成は各種エアバッグを開発し、グローバルに提供することを通じて、安全な車づくりに貢献してきましたが、今後も交通事故の被害者を減らしていくためには、エアバッグのさらなる普及と進化が不可欠です。それを支えるのが、30年以上にわたり培ってきたコンピュータによるシミュレーション技術(CAE※技術)です。
※CAE(Computer Aided Engineering)は、製品の設計・開発を支援するコンピュータシミュレーションシステム。製品や関連する物理現象をコンピュータ上で予測・再現し、構造解析、機構解析、流体解析などを行うことが可能で、新製品開発などの高効率化につながります。
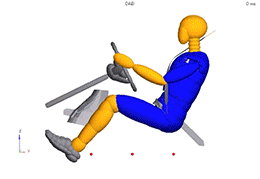
01全方位に対応
1989年に開発した運転席エアバッグから始まり、その後も側面衝突や後席乗員保護に対応した多種多様なエアバッグを製品化。あらゆる角度の衝突から車室内の人を守る360°フルカバーを実現しました。さらに対象を広げ、交通死亡者の多くを占める歩行者を保護するエアバッグの開発・量産も手掛けています。
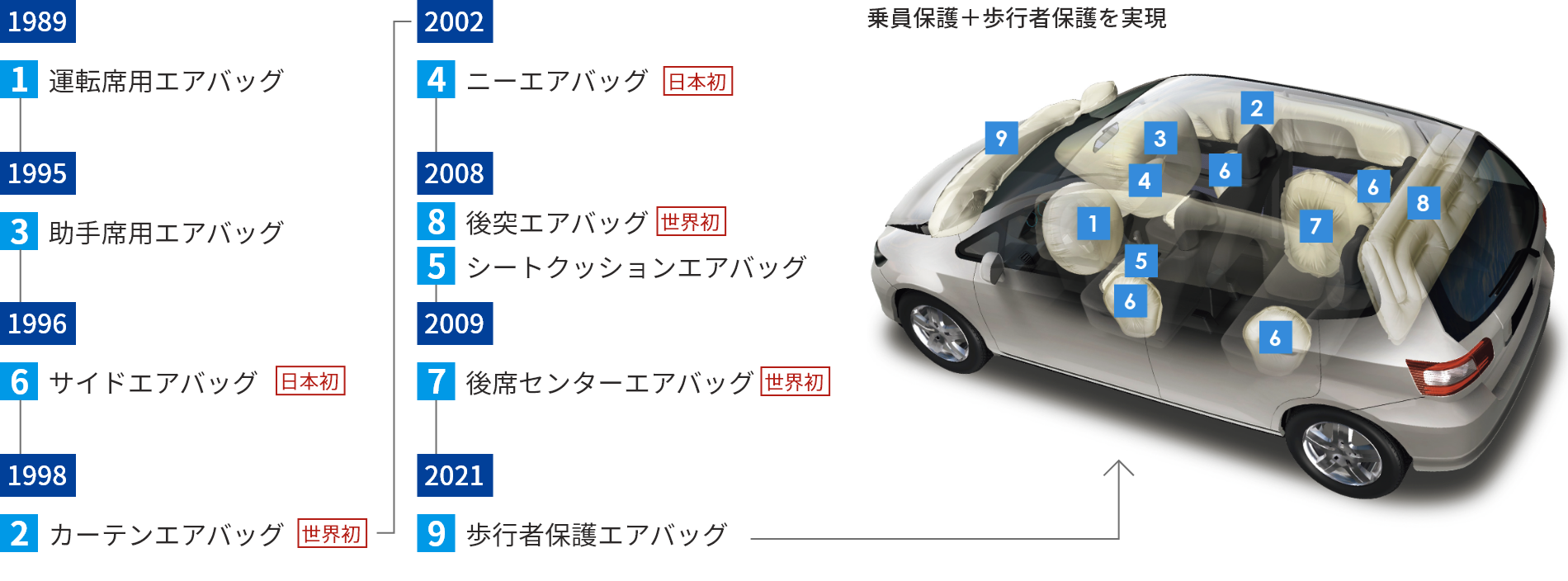
02実物での実験の積み重ねがブレイクスルーに
豊田合成は、1980年代からエアバッグの実用化に向けた実験を積み重ね、1989年に運転席用エアバッグの量産化に成功しました。同年には北島技術センター(愛知県稲沢市)内に実車の衝突を模擬する「性能評価実験場(スレッド試験場)」を設置。それまでのエアバッグ単体の実験・評価に加え、車両の衝撃吸収性能やシートベルトの性能などを車両全体の状況を加味して、衝突時の体の動きやケガの大きさなどを解析することが可能となり、車両レベルの安全性能の評価に取り組み始めました。そして2000年頃からは衝突時の乗員の動きを再現できるコンピュータによる解析を導入しました。
実車の衝突を模擬するスレッド試験
(現在は美和技術センター(愛知県あま市)で実施)

2009年頃からは技術の進化が本格化。開発にはシミュレーションの技術メンバーだけでなく、エアバッグの展開試験やスレッド試験といった現物の実験を担う性能実験メンバーや、エアバッグの設計メンバーなども加わり、エアバッグが展開していく過程を再現、高度化させていきました。エアバッグは折りたたまれた状態から乗員を受け止めるまで、時間とともにその形状が刻々と変化していくため、当時、コンピュータで再現するには大きな壁がありました。それを乗り越えられたのは、現地現物で実験を重ねて得た知見があったからです。
特に、エアバッグを膨らませるガスの流れを再現するのは困難を極めましたが、豊田合成は東北大学と協同で、インフレータからガスがどのように広がっていくのかを可視化することに成功。当時の技術では、エアバッグ内部のガスの流れは十分に再現できないと言われていましたが、2015年にシミュレーションの技術メンバーと性能実験メンバーの発想によってブレイクスルーを果たしました。実際のエアバッグの膨らみ方を再現するには試行錯誤を重ねる必要がありましたが、30年以上、地道に実験を繰り返し、エアバッグ展開に影響する様々な要因のリアルな動きを熟知していたからこそ実現できた技術でした。
実物による実験の知見を活用することで
エアバッグが開く際の「内部における実際のガスの流れ方」をシミュレーション技術で再現
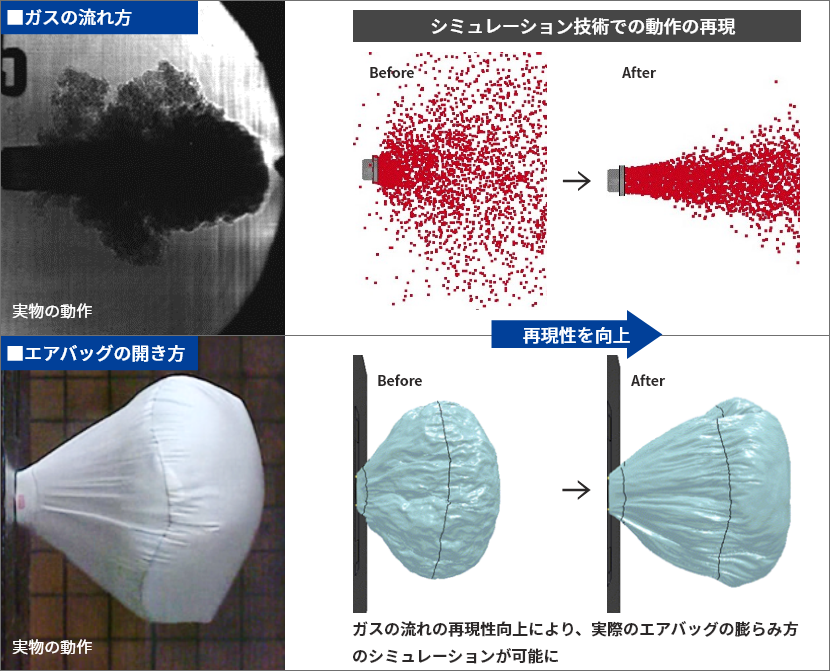
03技術の進化で安全で安心な次世代モビリティ社会へ
シミュレーション技術の進化により、衝突実験用のダミー人形だけでなく、実際のヒトを想定した再現・評価ができるようになりつつあります。たとえば、体つきのがっしりしている人や細身の人、背の高い人と小柄な人、子ども、さらには骨密度が低下した高齢者、妊婦など、「さまざまな体型の乗員」でシミュレーションできるようになることが期待されます。また、従来の安全試験では盛り込まれていなかった、斜め前方の車とぶつかる「オブリーク衝突」などの「複雑な衝突・事故形態」を想定した製品開発が実現します。さらにSUVや軽自動車といった「多様な車両形態」におけるエアバッグの開き方や乗員の受け止め方の評価も可能になります。
加えて、今後増えていく新しいタイプの車に対応した最適なエアバッグを社会に広めていく上でも、この技術はますます重要になります。急速に普及が進む電気自動車は、エンジン車とは車体構造が異なり、衝突時の衝撃吸収力が変化する傾向があります。また、自動運転車では、乗車姿勢やシートの位置の自由度が高まることが想定されます。このような車の変化に対応するには、新たなエアバッグの開発が不可欠です。豊田合成はそれをシミュレーション技術の進化で支え、これからも交通事故死傷者ゼロの実現に貢献し続けていきます。
技術の進化により、さらに多様な条件下での評価が可能に
-
様々な体型
子どもや高齢者、妊婦を含めた
多様な体型差への対応 -
衝突形態
今後、新たな安全評価基準として予想される
「オブリーク衝突」などへの対応 -
車両形態
SUV、軽自動車といった車両構造や
乗員数の違いによる変化への対応
開発者の声
進化の先にはエアバッグを試作レスで量産できる日も!?
エアバッグのシミュレーション技術はまだまだ序章です。人体の各部位の構造や性質をより忠実に模擬したシミュレーションやあらゆる事故状況をコンピュータ上にすべて再現できるようにし、今後も挑戦の手を緩めず進化させていきます。いずれは試作品を作らなくても最適なエアバッグを開発し、交通事故死傷者ゼロに貢献できるようになると考えています。さらに、蓄積したデータを元にAIで最適なエアバッグ形状を導き出せる時代を思い描きながら、これからも技術の開発に邁進していきます。
性能実験部 基幹技師 井田 等