当社はカーボンニュートラル、サーキュラーエコノミーの実現に向けて、2050年までにCO2排出量ゼロ、廃棄物を極小化する目標(TG2050環境チャレンジ)を掲げています。その実現に向け、ゴム・樹脂分野における幅広い知見と材料の配合技術や使いこなし技術を活かし、製品のライフサイクルを4つのフェーズ(「材料」「設計」「モノづくり」「回収・再生」)に分解して、具体的な取り組みを進めています。
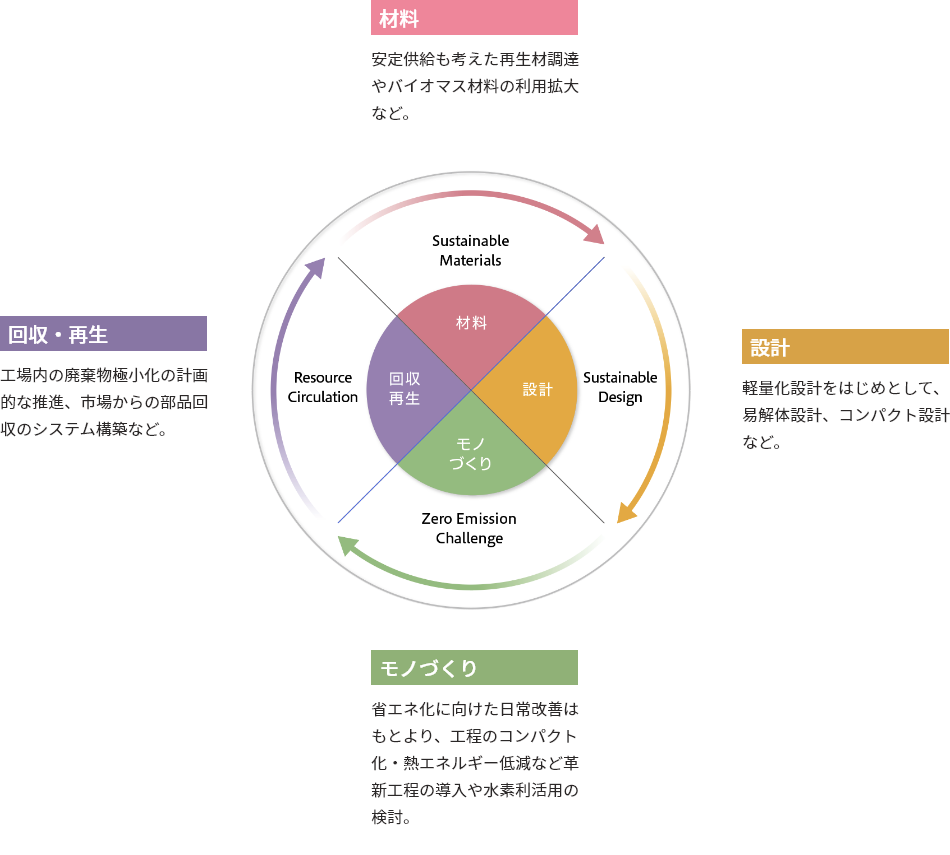
技術開発ロードマップ
材料開発、設計、モノづくり(生産技術)などを大きく変え、サプライヤーとも一体となり、様々な活動を行っていくことで自動車部品におけるカーボンニュートラルのリーダーを目指していきます。まずは、ゴムやプラスチックの廃材料のリサイクル化と再生材の製品へのマテリアルリサイクルを推進していきます。加えて、材料の使用量を減らす省材料設計、生産工程の省エネ化、さらにはバイオ材料への置換など幅広く取り組んでいきます。
-
01再生ゴム
脱硫再生技術
ゴムは、弾性を持たせる分子結合※を経て製品化するため、再生するのが難しい材料です。当社は、分子結合を切断して、再び原材料として使用できる状態に戻す「脱硫再生」において、独自技術を活かすことにより短時間で高品質な原材料に再生することを可能にしました。
※ゴム素材に硫黄化合物を混ぜて加熱(加硫)し、ゴムを構成する高分子と硫黄化合物を結び合わせている。
-
02バイオ材料
CNF※強化プラスチック
製品の環境価値を高めるため、当社の強みである材料技術を用いて各種バイオ素材の活用を進めています。その中でも、CNFはプラスチックなどに配合して補強材として使用すると、製品の「軽量化」や「自動車部品へのリサイクル」を可能にし、脱炭素・循環型社会を目指す上で有効な素材です。これまで、車の内外装に使われる汎用樹脂(ポリプロピレン)にCNFを配合した際の耐衝撃性の低下が、実用化にあたっての課題でしたが、当社は、材料の配合設計や混練技術により自動車部品に活用できる水準に高めました。
※セルロースナノファイバー。植物を原料とし、鋼鉄の5分の1の軽さで5倍の強度を持つ。
-
03新資源利用
水素貯蔵
水素は様々な資源から製造が可能であり、使用する際にCO₂を排出しないこと、再生可能エネルギー等を貯めて、運び、利用することができる特性をもっています。水素社会が広がっていくと、より効率的に大容量の水素を貯蔵するニーズが広がります。当社では既存の水素タンク技術をさらに発展させ、小型・大容量の貯蔵を可能とする水素タンクの開発も進めていきます。
-
04省材料設計
BEVらしい車室内空間の実現に寄与する
部品の薄型化当社は部品の軽量化を通じて燃費向上を図るため、ゴム・樹脂分野の知見を活かし、「薄肉化」「コンパクト化」「部品の削減」「低比重化」「発泡」といった省材料化に長年取り組んできました。これらの技術を活用し、近年ではBEV化などに対応し、広々とした車室内空間の実現を目指しており、コックピット部を薄型化・コンパクト化する開発を進めています。薄型インストルメントパネルに対応したエアバッグやレジスタなどを開発・提案しています。
-
05易解体※設計
運転席エアバッグ製品
従来、パッドと金属をリベットで組み立ていたため、完成前に一部の部材に不具合があった際に製品の解体ができず、不具合のない部材も含め全て廃棄せざるをえませんでした。製品の品質を損なわずに固定方法を変更し、容易に解体できる構造とすることで、部材ごと(樹脂パッド、布、金属)に分解できるようになり、リサイクルがしやすくなりました。
※色々な部品が簡単に取り外しできること
-
06省エネ化
塗装ブースのコンパクト化
ターンテーブル式で歩留まりを高める「トンボチルト塗装ロボット」を導入し、45%の省スペース化を実現。それによりCO2排出量を30%削減し、生産性向上と環境負荷低減を両立させました。また、製品の治具を常に上から下に塗料が吹き付けられるよう向きを変えられる構造にしたことで、塗装ロボットの可動域を減らし、塗料の粉じんを抑制。メンテナンス作業もしやすくなりました。
-
07排熱利用
工場排熱の活用
「熱電発電」は熱エネルギーを電気エネルギーに変換する発電方法で、CO2を排出しないエネルギー生産方法の一つです。2021年8月に熱電発電の独自技術を持つスタートアップ企業の株式会社Eサーモジェンテックに出資し、生産工程などで発生する排熱の有効利用に向けた開発を進めています。